Step 1: 'Watch' And Gather Intelligence Using Real-Time Visibility

Hidden costs from reusable pallet management arise out of pallet loss, bad utilization, and aging (lying idle in a warehouse or yard for weeks or months). Aging can also contribute to the loss of pallets. Pallets move across your own and customer facilities across cities, countries, and continents. Therefore, to watch what is happening with your reusable pallets, you need 360° supply chain visibility for a few weeks or for a few months to gather any valuable intelligence.
Let us have a quick look at the technologies that exist in the market to assist you with monitoring pallets, and which of them work the best:
a. Barcodes
Barcoding your returnable packaging is easy but scanning them accurately is close to impossible. Imagine you have 500,000 pallets and each pallet moves across your warehouse and customer facilities three times each month. That is 1.5 million scans at each location or a total of 1,250 person-hours or 52 person-days. Impractical, right? Therefore, barcodes cannot help, and are being replaced with better and more practical solutions.
b. RFID
RFID does not need ‘line of sight’ scanning like barcode does, but it is expensive to implement and needs proprietary readers installed at every warehouse. Further, there is no way to get visibility of pallets in-transit on trucks. You need to know if your trucker dropped off all your containers and goods. Therefore, RFIDs won’t solve your problem in terms of 360° visibility either, which brings Bluetooth into the picture.
c. BLE Beacons/Tags
Beacon-based technology, with portable gateway hotspots or a simple smartphone, could help you. This technology is easy to implement with no upfront infrastructure setup costs, works at the warehouse and in-transit (using the portable hotspot gateway or smartphone), and costs much less than RFID. Beacons or BLE tags have a battery life of a year or more, and can carry additional sensors for tamper, temperature, etc. to monitor your packaging’s location and even report its condition.
See why BLE Beacons trump older technologies like RFID.
But guess what, technology has gone beyond the infrastructure-light BLE tags too! It has already moved on to ‘infrastructure-less’ tracking technology. There is now a way you can eliminate the need for a gateway. Read on to know.
d. Multi-LPWAN Tags (Nb-IoT, LTE-M, Sigfox)
Imagine having a hundred thousand sensors sharing data without any reader installations at facilities, with years of battery life, AND all that at a lower expense! All you have to do with these LPWAN tags is attach them to your returnable containers. The tags are good on their own, as they don’t even need a hotspot gateway setup, which makes it an infrastructure-free arrangement. What could be better than simply placing the tags on your RSAs (Returnable Supply Chain Assets) without the effort, expense, and time-consuming infrastructure setup!
Once you have visibility of pallets, bins, tubs, or small containers across your supply chain for a few weeks or a few months, you will be able to see how they move, where they are lying at any point of time, and their aging data. This helps formulate the basis of estimating the hidden spend you are incurring on returnable packaging management today.
Step 2: 'Calculate' Your Savings
Once you have the visibility, you will be able to identify and estimate the impact of various inefficiencies in pallet movement across your supply chain. Let us have a look at four areas where you could have inefficiencies contributing to your financial leakage.
a. Pallet Loss – How to Estimate?
Pallet loss can happen either in transit, or at yours or your customer’s warehouse. With visibility using LPWAN tags, you can prevent almost 100% of your pallet loss. Aging is a major factor that contributes to pallet loss. This is because when a pallet is lying unutilized, it could get worn off over time or stolen.
Your total savings on pallet loss can be calculated as follows:
Pallet Loss Savings (A) = Cost of Pallet – Portion Paid by Insurance During a Claim – Deductibles or Co-pays
For example, if your pallet costs $50 and your insurance company pays you 90% of your claim with a deductible of $5 per claim, then the total savings for you is $10 per pallet. If you are losing 100,000 pallets every year, this is an immediate savings of $1 million for your business.
b. Pallet Utilization – How to Estimate?
Pallet utilization is 100% when the aging of a pallet is 0 days, which means that the pallet is never kept idle. Though in reality, due to challenges in arranging for the reverse logistics for your pallets, loading and unloading delays, and unforeseen circumstances, pallets do age for a few days in a year. Hence, aging beyond an acceptable range can increase your costs.
Therefore, you can estimate your savings as follows:
Savings Through Better Pallet Utilization (B) = (New Number of Days of Use Per Pallet in a Year - Old Number of Days of Use in a Year) x Cost Per Day
For example, if a pallet costs you $0.50 per day in terms of rental, the early number of usage days was 300, and you now bumped it up to 360 days, the savings for you
is 60 days of use or $30 per pallet. This translates into an annual savings of $7.5 million if you had 250,000 pallets.
c. Saving “Lost Days in Shipping” & Associated Working Capital Due To Unavailability of Pallets When Needed
Without the visibility of pallets, it is hard to plan to have pallets ready for shipping an order. How do you calculate the loss this has made to your company?
Let us consider the number of days your goods have awaited pallets for shipping as ‘C’.
The total value of your goods that awaited the pallets is ‘D’.
Your Interest Rate is ‘E’% Per Annum.
Working Capital Interest Savings (F) = (D x E% x C/365)
For example, if you had 5000 consignments each worth $250,000 and you saved a 2-day delay on each, your savings on Working Capital Interest at an interest rate of 5% is $68 per consignment or $340,000 annually.
d. Saving “Lost Days in Shipping” & Associated Detention Cost
Saving lost days can also save you on the detention cost your logistics service provider might charge you for idling the truck or rake at your facility.
Detention Savings (G) = Cost Per Day of Detention x Number of Detention Days Billed by Your Logistics Service Provider
Total Savings (H) = Sum (A, B, F, G)
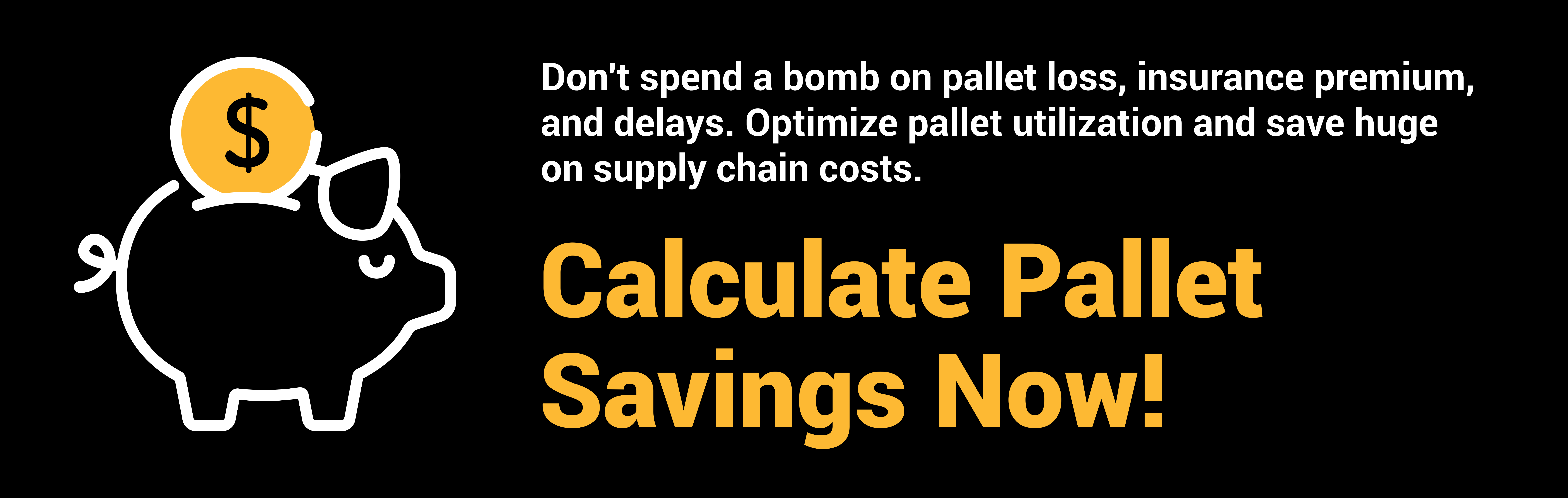
By knowing your potential total savings, you are in a good position to attack your problem. With this ammunition in your hand, you can now implement a smart pallet management program using real-time visibility.
Step 3: “Attack” by Building a Process with LPWAN Visibility
a. Set Aging Thresholds
Set a threshold for aging and configure alerts using your LPWAN tagging solution when a pallet ages beyond its threshold.
b. Plan Better Routing
Build a supply chain plan around the movement of your pallets. It is not easy, but once done it will ensure that your pallet aging reduces, and utilization improves – leading to the decrease in instances when you are unable to ship your goods due to the unavailability of pallets.
c. Plan in Advance For Reverse Logistics of Pallets
With LPWAN tags you will have complete visibility of the pallets at different locations in your chain of custody – at your warehouses, in-transit, and at customer sites. Using this information, you can plan to consolidate your stranded pallets with other pallets at various locations, plan their routing, and come up with a reverse logistics strategy even before a pallet gets shipped to a location from your warehouse.
Find Your Net Return-On-Investment (ROI) Before Implementing LPWAN
To get the net savings calculated from pallet loss recovery, utilization, and lost shipping days, you will need to factor in the cost you will be investing in your LPWAN tagging solution. The solution investment cost will include the cost of the tags and integrations with ERPs or WMS, if any.
Assuming that cost is (I), the overall return on investment (ROI) for you will be:
Net ROI = [Total Savings (H) – Cost of the LPWAN solution (I)]
It is also important to note that the savings calculations could vary by industry or use-scenario but on an average, your ROI on LPWAN could be about 5-10 times as much as that of RFID. Your payment terms or capital borrowing deals with your financial institutions can also affect working capital calculations. The detention cost varies based on your agreements with your logistics transporter providers.
In such a situation, it warrants getting an expert to look into your savings estimates. Schedule a free web-consultation with a Roambee solution expert! Along with your free savings estimate on your supply chain assets, you will learn how the industry’s first pay-as-you-go LPWAN-based infrastructure-free monitoring solution works indoors, in-transit, and outdoors!